If your business manages product inventory or fulfills orders within a supply chain, you are likely already acquainted with the concept of warehouses. These critical storage facilities house items for stocking, packing, and shipping on behalf of brands, wholesalers, manufacturers, and other exporters… and they will continue to evolve in the days ahead.
That said, there is a good chance you have already partnered with a warehouse or are looking to do so in the future now that the COVID-19 pandemic has pushed Ecommerce into overdrive. Whether you are a B2B, B2C or D2C operation, choosing the right warehouse is essential for optimizing your business, fulfilling customer orders, optimizing your distribution process, and safeguarding your inventory directly.
“Warehousing” is a pretty general term for such a critical component of your operation. Let’s take a closer look at what warehousing means, the pros and cons of it, and how to choose the best warehouse model in 2022.
Contents
What Is Warehousing? Why Does It Matter?
Whether your inventory requires more storage space, existing warehouse conditions are damaging your products, or you simply desire a more advanced facility for managing inbound and outbound logistics, it is important to understand the various elements within “warehousing” and their impact on your overall business strategy before choosing one.
Warehousing refers to the process of storing physical goods in a dedicated warehouse or facility until they are sold or distributed. In a sense, it is a blanket term for several major functions:
- Safely and securely storing and organizing products in a way that is easy to navigate;
- Mapping where specific items are located within the facility;
- Tracking arrivals, how long items have been in the warehouse, the quantity and quality of those items, and any outbound shipment information;
- Ensuring order fulfillment for positive buyer experiences; and
- Providing timely, logistical data to employers about their inventory.
Warehouses are similar to fulfillment centers, but they do not experience as much traffic or item turnover. Such centers typically depend on third-party logistics and a strategic geographic placement to ensure inventory remains stocked and orders are filled at a rapid rate. For example, food distributors may need their products received and shipped out within a day, so a traditional warehouse would not be appropriate.
Consider the pros and cons of warehousing, if you are unsure if your business is ready to take the next step:
Pros of Warehousing: allows your business to expand, can keep inbound and outbound logistics organized and efficient, can boost labor productivity while cutting down on human error, and ensures unique product needs and orders are fulfilled (ex. temperature controlled spaces, individual orders, etc.).
Cons of Warehousing: your product is no longer necessarily in your direct possession; the wrong warehousing partnership could be harmful to order fulfillment and customer satisfaction; choosing the wrong partner could affect your brand identity; it can be expensive.
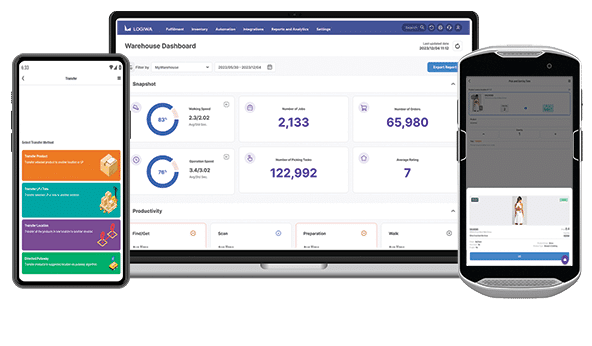
Primary Types of Warehouses
Warehousing is simple enough to understand, but picking the right facility can be a challenge. After all, there are many different kinds of warehouses, all of which may have their own unique approach to fulfilling operational needs.
Each warehouse has a specific industry, target market, budget, or product type that it is best suited for. Here is a brief overview of the most common warehouse types:
- Public warehouses: Public warehouses are owned by federal agencies but are made available to private sector companies. If you are a small or medium-sized business (SMB) and only need to store goods for a short period of time, a public warehouse offers the most affordable option. They may not necessarily have the advanced technologies other warehouses do, but they are a great place to begin.
- Private Warehouses: Private warehouses are typically owned by wholesalers, distributors, manufacturers, and online marketplaces who are established. Although they are usually more expensive than public ones, private warehouses are still a fine option for growing Ecommerce businesses trying to become a major, long-term presence in a specific region.
- Bonded warehouses: Bonded warehouses store imported goods and safeguard them from customs duties for a period of time. By using customs bonds to rent a space, you ensure you do not face unnecessary financial losses for products that have not yet sold. Using a bonded warehouse means you would not have to pay duties on goods until they are released from your facility to a buyer. Restricted items can also be stored until the proper paperwork is completed. These warehouses are ideal for Ecommerce businesses that specialize across international lines and care deeply about security.
- Smart warehouses: Smart warehouses are storage facilities where the storage, fulfillment process, and organizational management are managed with artificial intelligence (AI). Automation using AI allows robots and drones to perform tasks like packing, weighing, transporting, and storing goods. Corporations like Amazon use these types of facilities, and have invested heavily in automating their processes to remain a top competitor. Amazon warehousing, as a model of smart warehousing, is a perfect example of AI making inbound and outbound order fulfillment faster and less prone to human error.
- Consolidated Warehouses: Consolidated warehouses take small shipments from different suppliers and groups them into larger shipments for distribution. With consolidated warehouses, all the shipments are intended for the same geographical location, so it is an economical way of satisfying orders. The overall financial investment and volume of inventory required to partner with these warehouses are affordable, making them a great option for budding operations.
- Cooperative Warehouses: A cooperative warehouse is owned and run by joint or allied organizations. An example of this might be a farm and winery working together. Both members and those outside the co-op would be able to store goods at the cooperative warehouse facility, but co-op members would have the perk of paying reduced rates.
- Government Warehouses: These warehouses are directly owned, controlled, and used by federal agencies for a multitude of reasons. These might include a manufacturing warehouse for an Air Force base or a seaport storage facility. Typically, government warehouses charge low rates, as well. However, if you are unable to pay rent on time, the government retains the authority to recover their rent by disposing of your goods.
- Distribution Centers: A distribution center is a storage space that is built with specific holding and distribution parameters in mind. Items that roll through these centers are temporary and get exported more quickly than most other warehouse items. Put simply, distribution centers take in a lot of inventory and distribute to resellers and retailers in the shortest amount of time possible. An example of this would be food and perishable items needing to be re-distributed within a day.
Imagine, your warehouse labor costs are cut by 70%. Your warehouse operates during the day and night with equal costs. Your inventory counts are updated daily. Learn more about Locus Robotics.
How to Choose the Right Warehouse
With COVID-19 pandemic forcing consumers to adapt, Ecommerce has exploded and placed new pressures on employers to meet demand. To succeed, you need know your product is in good hands and stored in the best warehouses possible.
Once you know the type of warehouse that best fits your business, you can narrow your options down further by assessing the following:
- Total space available and cost (storage costs);
- Logistical insights offered via software solutions;
- Effective technology for organizing, picking and receiving inventory (ex. using SKUs);
- Safety and security measures in place within the facility;
- Whether or not the warehouse maintains a dependable, trained staff;
- Accessibility / proximity to your target markets;
- Unique facility design features (appropriately designed interiors, temperature control, etc.);
- Quality controls for protecting the integrity of inventory items;
- Customer service reputation;
- And more!
Every employer wants to make the best decisions for their business, and itis a critical ingredient for future success in the Ecommerce world. Now is the time to assess your options or give your current warehouse management system a revolutionary boost. Check out Logiwa’s cloud WMS Solution for more insights on leveraging warehouse logistics and securing optimum order fulfillment.
Run a digital fulfillment network and grow your DTC business–without additional headcount
3PL
Cloud 3PL software for high-volume fulfillment excellence