In this article, we’ll dive into the significance of effective labor planning in warehouse operations, emphasizing that the right workforce is pivotal for efficiency and customer satisfaction. Through this read, we’ll guide you on how to navigate the challenges of labor shortages, the importance of strategizing for future hurdles, and the role of technology in optimizing labor planning.
Key Takeaways:
- Proper labor planning is crucial for warehouse efficiency and customer satisfaction.
- Labor shortages are a pressing issue, with 73% of warehouse operators struggling to meet their labor needs.
- Effective labor planning starts with data, understanding your current workforce, and future operational requirements.
- Calculating the churn rate provides insights into employee turnover and informs hiring strategies.
- Leveraging technology can significantly enhance labor planning processes.
Regardless of the size of your warehouse operations or the number of orders coming in through your ecommerce channels, there’s one commonality between all fulfillment operations: the importance of proper labor planning. After all, your employees are your greatest asset and a failure to have the right number of workers or skills supporting your business can make or break warehouse efficiency and customer satisfaction.
For manufacturers and warehouse operators, labor shortages and competitive labor sourcing have become the new reality. According to Modern Shipper, 73% of warehouse operators cannot source enough labor to meet the needs of their business. Moreover, Capstone Logistics reported that the average churn rate for warehouse associates is 60%.
Labor shortages aside, warehouse labor planning is an important process that helps you prepare for future challenges, analyze employee competencies to ensure goals are met, and reduce costs stemming from ineffective hiring processes. Let’s break down three easy ways to improve labor planning, as well as how to attract and keep top performing employees.
In this blog, we’ll help you understand:
Step One: Create a Staffing Plan
A major factor in successful labor planning is data. You need to be able to take stock of your current labor force, as well as your future operational needs in order to make an effective labor plan. Informed decision-making starts with evaluating where your operations stand and the direction you want to go. Once you know that, you can build out an ideal staffing plan unique to your business.
Start by calculating your churn rate. This helps you understand the overall turnover of employees as your existing employees leave and new ones get hired. Understanding this percentage provides a foundation for planning needs and insights into how aggressive your hiring efforts need to be. If you conduct exit-interviews, this would be the time to investigate what’s motivating your employees to leave.
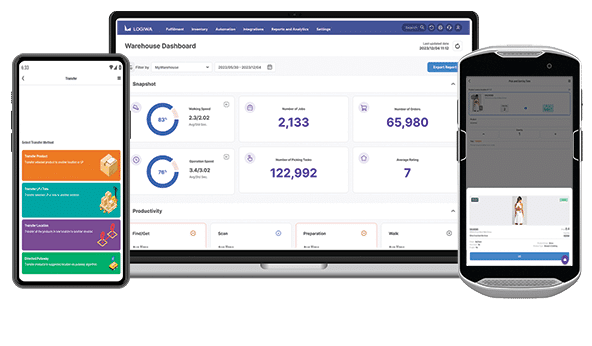
Next, you will want to identify the following:
- The roles and responsibilities present in your warehouse
- Estimated labor hours and shifts for each position
- Fluctuating labor needs based on seasonality
- Anticipated training and certification requirements for each position
- Benchmarking and forecasting (projected growth and projected products)
This information gives you a framework for your entire operation and makes it clear where the holes in your operations remain. From there, you can begin focusing on internal warehousing and recruiting processes for creating the best workforce possible.
Looking for more information on labor planning? Download our guide, “5 Steps to Success Warehouse Labor Planning.”
Step Two: Account for Operational Factors
Your current workforce and available hiring pools will affect your staffing decisions, but you must also consider the conditions of your operations. To be more specific, it is beneficial to labor plan based on the following:
- Your customers and how their needs may change: B2B operations often require fewer staff with more certifications, while high-volume B2C/DTC operations need more human capital for picking and packing operations.
- The types of products you’re managing: Depending on how your item orders are received or if they are single vs. multi-order will affect the number of people and labor hours required for the order fulfillment process.
- The technology available to your warehouse employees: Investing in warehouse management systems (WMS) solutions with productivity-geared applications like directed putaway or intelligent picking and packing algorithms will affect the total number of employees you need and the roles needed at your fulfillment centers. If you’ve implemented robotics, your staffing plans will also be affected.
- Warehouse layout and storage systems: If you’re using Put Walls or multi-tier organizational systems, or moving a high volume of inventory in and out of your warehouse, your workflows will play a factor in determining how many employees you can have on the floor or a specific area at one time. Plus, with smart warehouse setup, you can 65% increase order volume processing without adding headcount.
This blog is part of Logiwa’s 15-minute QuickTake webinar series. To view the recording of “Warehouse Labor Planning for High-Volume Fulfillment”, or any of our previous QuickTake sessions, visit: Logiwa Resource Page
Step Three: Use Technology to Your Advantage
Technology can be overlooked as an area of labor planning, but it supports recruiting and employee retention. Easy-to-use onboarding technology and competitive automation solutions are a great attractor for many job-seekers. Here are a few of reasons technology may appeal to your existing and future employees:
- When you implement tech properly, you create a safer and happier working environment.
- Robots complement existing operations and can act as a supplement workforce, meaning less risks and less walking for your warehouse staff, and drones can reach hard-to-reach places without added hassle.
- Inventory management technology like barcoding helps with speed and inventory accuracy, so employees can find what they need with ease.
- Integrated dimensioning and weighing tools help fulfillment operations flow seamlessly, eliminating unnecessary delays, work, and frustration.
With the right WMS in place, you can use your historical records and current growth trends to anticipate and plan for your labor. For more information on Logiwa’s Cloud fulfillment platform, visit: www.logiwa.com/request-a-demo.
FAQs: Warehouse labor planning
Q: What is the importance of warehouse labor planning?
A: Warehouse labor planning is vital for ensuring high-efficiency in fulfillment operations and achieving customer satisfaction. Proper planning ensures that there are the right number of workers with the necessary skills to support the business.
Q: How prevalent are labor shortages in warehouse operations?
A: Labor shortages are a significant concern in warehouse operations. According to the article, 73% of warehouse operators cannot source enough labor to meet their business needs.
Q: What factors play a role in successful warehouse labor planning?
A: Successful warehouse labor planning relies on data-driven decision-making. It involves evaluating the current labor force, understanding future operational needs, and creating an ideal staffing plan tailored to the business.
Q: How can I improve my warehouse labor planning process?
A: The article suggests three steps to enhance warehouse labor planning: 1) Create a comprehensive staffing plan, 2) Account for operational factors, and 3) Utilize technology to gain an advantage in planning.
Q: Why is understanding the churn rate important in warehouse labor planning?
A: The churn rate provides insights into the overall turnover of employees. By understanding this percentage, businesses can plan their hiring efforts more effectively and investigate the reasons behind employee departures.