Implementing a new warehouse management system (WMS) can be tremendously beneficial for B2B, DTC, and hybrid fulfillment operations. From optimized warehouse efficiencies and labor management to improved cost-savings and customer satisfaction… Finding the right WMS is key to achieving fulfillment excellence and long-term growth.
But before you can enjoy the benefits of a high-efficiency WMS, you first have to successfully implement it. And having a pain-free WMS implementation, one that does not halt operations or lead to costly delays, is easier said than done. According to Gartner Research, while most WMS implementations are successful, about 30% of operations suffer delays and nearly all experience setbacks.
As a retailer, online seller or third-party logistics (3PL) provider, you do not have the luxury of slowing down and making mistakes – especially not for the average 6-8 month timeframe it takes to implement a standard WMS system. Many ecommerce operations would rather sacrifice profits and efficiency than risk the outcomes of a failed implementation. Luckily, streamlined implementation has become a new industry standard.
Executing a successful WMS implementation is important for avoiding setbacks and major delays for today’s fulfillment operations. Consider Logiwa’s seven expert tips for ensuring a positive WMS implementation free from disruptions.
The 7 tips to ensure a successful WMS Implementation are.
- Choose a cloud-based WMS
- Leave nothing out when ensuring a WMS is aligned with your unique workflows
- Audit WMS functionalities against your process requirements before committing
- Test as long and as many times as needed
- Check the real-life effects of your WMS on your facility
- Plan for the cultural shift by creating experts on your team
- Ensure proper Go-Live support
#1: Choose a cloud-based WMS.
Adopting a cloud WMS platform (as opposed to an on-premise solution) is ideal for avoiding complex, expensive disruptions that often arise with legacy hardware systems. With cloud-based solutions, not only does implementation take a fraction of the time, but issues can be flagged and resolved with far greater efficiency thanks to the live network visibility created early on.
As you work out the kinks in your cloud WMS, you and your WMS provider are able to monitor and address problems together as they arise. This digital approach to implementation ensures the rest of your operations can continue without delays, even while you continue to tweak systems or work out which workflows and algorithms need adjusting. This, in addition to the fact that some cloud WMS solutions can be implemented in as little as 4-6 weeks, makes cloud WMS solutions ideal for easier implementations and avoiding disruptions.
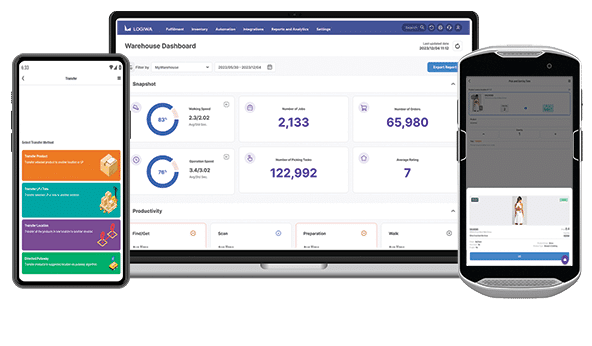
#2: Leave nothing out when ensuring a WMS is aligned with your unique workflows.
Securing your best-fit solution and a trusted WMS provider before you start the implementation process may seem obvious, but many operations mistakenly sign off on impressive solutions only to discover they cannot satisfy their desired functionalities. Make sure each one of your business processes is captured with great detail as you finalize your WMS selection, so there is no uncertainty about whether the WMS provider’s features can support your requirements.
Take time to list all the critical processes that are part of your operation to ensure no surprise gaps occur once implementation is underway. Processes that cannot be handled by the WMS (and that do not have manual workarounds) will not only limit the success of your WMS, but lead to ongoing complications and setbacks once you are operating beyond implementation. In order to avoid major disruptions to your operations – ensure you and your WMS provider go process-by-process to review and confirm the solution is the right one for your business.
#3: Audit WMS functionalities against your process requirements before committing.
Once you have compiled your list of requirements to provide to your WMS provider, they will be able to give you a formalized proposal covering the specific functionalities they will be able to provide. This may include manual alternatives and customizations based on the requirements you submitted, as well as suggested alternatives for improving your established operational processes. Either way, a secondary audit can go a long way towards ensuring you and your future WMS are compatible.
No solution is perfect, but you should be able to have concrete processes and evidence that your implementation will have the desired outcome for your business instead of prolonged, unwanted disruptions to your order fulfillment. Make sure this step is taken before you sign off and get started with your WMS solution. As a best practice, ensure all your desired customizations are built into the WMS software before you even begin implementation.
#4: Test as long and as many times as needed.
Testing all levels of system functionality is key to avoiding disruptions in your fulfillment network and business processes. That includes holding your provider and team accountable for successfully carrying out systems readiness testing and verifying the visibility and accuracy of your new WMS reporting functions. In addition to basic data conversions, your provider should be conducting ample testing on: basic system functionality, interface connectivity (integrations), user acceptance testing, and more.
If there is any doubt in your mind that an integration is not functioning right (perhaps your WMS and ERP system are not exchanging data as easily they should or your digital inventory counts don’t match your physical count), the solution is simple: flag the issue, make appropriate adjustments, re-test, and process results until processes are flowing flawlessly. No matter how long this takes, testing prevents more significant disruptions down the road.
#5: Check the real-life effects of your WMS on your facility.
The impact of WMS implementation on your warehouse floor layout, storage and inventory levels, and workflows should be easy to predict with the right planning. However, once your custom automation rules are actively working to optimize your warehouse space utilization and smart putaway algorithms are reorganizing racks, palettes, etc. for optimum efficiency – there is a chance that certain inventory items may be exceptions to the rules. It is better to stay cognizant of these issues rather than handling them in retrospect.
As you move through each phase of WMS implementation, remember to continuously evaluate the health of your facility as well as your software: Do certain products have enough room? Are replenishment and smart putaway items working effectively? Make a plan for this during the testing phase, as well as during and post go-live.
#6: Plan for the cultural shift by creating experts on your team.
Training all of your employees is necessary to avoid disruptions. Every one of your employees needs to know how to use your system at some basic level to eliminate the possibility of ever being short-staffed and underprepared to handle your new WMS. Halting operations or slowing down while you wait for someone who knows how to use the system creates costly delays.
Test your employees on their user comprehension, while helping certain members of your staff become superusers and trouble shooters. Even if you have the best WMS support team in the world, you must be able to access and perform any error-correcting tasks yourself in order to guarantee zero downtime for your operation. Having trouble shooters that can cover specialized processes within the system (ex. putaway, picking and packing, order routing, etc.) also ensures you have more than one expert on standby to help your team transition through implementation hiccups.
#7: Ensure proper Go-Live support.
Implementation requires support from your WMS provider to ensure success, and the go-live phase is not any different. The moment your WMS is helping process live orders and route orders to the correct workflows, anything could happen. No matter how successful your testing phase was, bugs can still arise. For that reason, you should know exactly how to escalate problems to your technical support team and communicate with your provider for any needed assistance in resolving problems.
At Logiwa, we understand the catastrophic effects of halting operations due to unexpected malfunctions and system-related setbacks. That’s why we lead our clients through a four-stage implementation process and even help them process their first order. In addition, we provide ongoing training post go-live to ensure the best implementation experience possible. Learn more about our approach to WMS implementation by reading some of our customer success stories.
Run a digital fulfillment experience with a fully integrated Cloud-Based WMS System
Warehouse Management
Modern digital WMS powers a modern fulfillment experience