In this guide, we’ll help you better understand what goods in transit are, their significance, and the importance of tracking them. We’ll also share proven tips for effectively managing such goods to optimize warehouse management and performance.
First, here are the five key takeaways about goods in transit:
- Goods in transit will remain a part of your inventory until your customers receive them. It’s important to treat them as such.
- Failure to track goods in transit and verify they’ve reached customers may lead to inventory miscalculations and losses.
- Goods in transit can fall under FOB Shipping Point (the purchaser is liable once the goods leave your warehouse) or FOB Destination (your warehouse is liable for the goods until you complete delivery).
- Inventory accounting is invaluable to effectively managing goods in transit.
- One way to streamline goods in transit management is by implementing an inventory management platform such as Logiwa WMS.
Contents
A Look at Goods in Transit
Goods in transit are processed and shipped products on the way to customers from your warehouse. These products remain goods in transit until the client or purchaser receives them.
Your warehouse should track and account for goods in transit just like it accounts for inventory within your facility. Otherwise, your facility may experience issues like inventory miscalculations or losses.
Examples of Goods in Transit
To paint a clearer picture of what goods in transit are, let’s look at what such goods look like in third-party logistics (3PL) and ecommerce warehouses.
3PL Warehouse
A 3PL warehouse (like DHL) is a third-party company that stores and distributes order items on behalf of other businesses. The 3PL warehouse will ship orders on behalf of its clients to specific recipients. While an ordered item is in transit, it remains part of the client’s inventory. The order becomes completed after the recipient acknowledges receiving it.
Ecommerce Warehouse
Ecommerce businesses (think Amazon) ship orders to customers from a warehouse. Depending on the order, customers may have to sign to acknowledge receipt. Alternatively, the delivery driver will drop the item in a secure location, and the customer will receive a delivery confirmation email.
Once delivered, goods in transit become a completed order, and the warehouse can deduct the item from its inventory list.
The Significance of Goods in Transit for Warehouses
Neglecting to track goods in transit can lead to several potential issues for warehouses and their customers. The biggest of these issues include:
- Loss of goods: Ineffective tracking of goods in transit increases the likelihood of stolen or misplaced goods. Since the warehouse is liable for the goods until it reaches the purchaser, frequently losing goods in transit can negatively impact revenue.
- Unhappy customers: If you don’t track goods in transit, you can’t give customers accurate updates regarding delivery ETA or order location. Delivery delays without shipping updates can upset customers, leading to negative reviews that ruin your brand reputation.
- Poor inventory control: Properly tracking goods in transit will reveal completed and uncompleted orders. You can use these insights to plan inventory and prevent overstocking and stockouts.
- Missed opportunities: Monitoring goods in transit provides valuable insights into supply chain performance and demand patterns. The insights can help you identify opportunities to improve and optimize shipping and other warehouse processes.
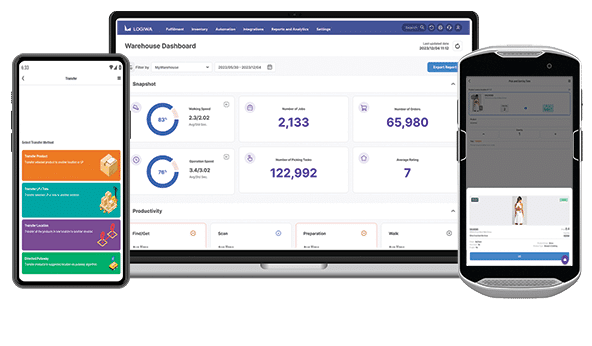
6 Tips for Effectively Managing Goods in Transit
Monitoring goods in transit is crucial for effective inventory control. To support you in properly managing the goods that aren’t in your warehouse, here are some best practices.
#1. Implement Inventory Management Software
Manually monitoring inventory can be time-consuming, inefficient, and inaccurate. A better solution is inventory management software for automatically monitoring inventory levels and receiving stock updates.
However, inventory management solutions are not equal. If you want an easy-to-use tool that provides accurate, fast, and valuable insights, you can’t go wrong with Logiwa WMS. The platform can double as your real-time ecommerce inventory management and cloud order fulfillment software.
The platform will sync inventory levels between goods in transit and goods within your warehouse so you know everything going on with your inventory. Whether you are a B2B, 3PL, or D2C warehouse, Logiwa has solutions for optimizing stock levels and avoiding costly stockouts or overstocking.
#2. Take Advantage of Automation
The best inventory management tools, such as Logiwa, provide automation solutions for monitoring goods in transit. For instance, Logiwa can automatically compare carrier rates and providers, so you can pick the most effective and affordable shipping option to complete orders and reduce transit times.
You can also use the platform as your ecommerce shipping software to provide customers with automatic shipping status and location updates.
#3. Integrate All Inventory Data
A WMS like Logiwa can serve as your single source of truth where you can monitor and leverage inventory data from various systems. Having all your data in one location simplifies finding the information you need.
Also, integrating Logiwa with other warehouse systems ensures continuous data synchronization, giving you access to only up-to-date, real-time data. Plus, the automatic and continuous synchronization between systems connected to a single source of truth eliminates issues caused by double or wrong data entries.
Up-to-date and accurate data will support you in tracking goods in transit, providing customer updates, and accounting for inventory.
#4. Understand Who Owns Goods in Transit
Who owns goods in transit depends on if you have a freight on-board (FOB) shipping point or freight on-board (FOB) destination arrangement. A FOB shipping point setup transfers ownership to the purchaser once the goods leave your warehouse for shipping.
On the other hand, an FOB destination setup means your warehouse owns and is liable for goods in transit until the purchasers take possession.
The owner of goods in transit is responsible for losses that may occur during transportation due to accidents, errors, or theft. The owner must also financially account for their goods in transit, so it’s critical to understand who’s responsible.
#5. Carefully Account for Goods in Transit
Accounting for goods in transit is two-fold. First, you must “account” for them financially on your financial statements. Goods in transit are considered to be current assets, so you’ll need to be sure and list them on your books for accurate accounting.
Second, you must “account” for them as part of your inventory for accurate inventory management. While goods in transit are still considered a part of your inventory, they’re not available for new orders. You’ll need an inventory management system that can track goods in transit to ensure accuracy.
#6. Utilize Transit Warehouses
Transit warehouses offer a temporary place to hold or store shipped goods before sending them to their final destination. You can leverage transit warehouses to consolidate orders before sending them to purchasers.
For example, if a purchaser’s order contains items from multiple facilities, you can ship orders from the facilities and consolidate them at the transit warehouse. After consolidation, you can send the ordered items together to the purchaser.
Consolidating goods in transit simplifies tracking and managing multiple items heading to one place. It’s also cheaper than shipping order items separately to fulfill one order.
Manage Your Inventory with Ease with Logiwa WMS
Effectively managing goods in transit can be a challenge, especially for large warehouses. Fortunately, with a WMS like Logiwa, you can easily monitor goods in transit and get automated updates regarding orders. Plus, Logiwa WMS offers valuable, easy-to-understand insights for improving inventory management and shipping.
But don’t just take our word for it. Request a demo of Logiwa WMS today to see its abilities within your own warehouse.
FAQs about What are Goods in Transit
What are goods in transit?
Goods in transit are purchased, processed, and shipped products on the way to customers from warehouses or distribution centers. These products remain goods in transit until the client or purchaser receives them.
Who owns goods in transit?
Who owns goods in transit depends on the freight on-board (FOB) shipping point or freight on-board (FOB) destination arrangement. A FOB shipping point setup transfers ownership to the purchaser once the goods leave your warehouse for shipping. A FOB destination setup means your warehouse owns and is liable for goods in transit until the purchasers take possession.
Are goods in transit included in a purchase inventory?
Yes, goods in transit are part of a warehouse’s purchased inventory. Operators should track and account for goods in transit just as they would for inventory within their facility. Otherwise, issues like inventory miscalculations or losses arise.
What is an example of goods in transit?
Finished goods in transit to a warehouse from a supplier, purchased merchandise that has left a warehouse on its way to a seller location, and packaged orders on its way to consumers via carrier can all be considered examples of goods in transit.
Modern cloud fulfillment software built specifically for B2C and DTC fulfillment
Warehouse Management
Modern digital WMS powers a modern fulfillment experience