In this guide, we’ll define the warehouse put wall, discuss its benefits, and provide guidance on how to get started. But first, here are five key things to know about put walls:
- Put walls are storage systems tasked with supporting order consolidation and sorting after batch picking.
- Advanced put wall systems include assistive technologies that support sorting operations, such as Put-to-Light systems and robotics.
- Put walls have many benefits. For example, they boost efficiency and order accuracy across your warehouse.
- When deciding whether to implement a put wall, you must consider three key factors: order volume, product dimensions, and the physical layout of your warehouse.
- To get started, you must decide on a put wall system, map out your workflows, and ensure your WMS can integrate with a put wall system.
In this guide, we’ll discuss:
What Are Put Walls?
Put walls are dedicated storage systems aimed at supporting order consolidation and sorting processes after a batch picking run. They help streamline the picking and packing process by providing a location for pickers to unload unsorted inventory, which allows for a follow-up sorting process to consolidate orders even more efficiently.
Put wall systems vary in style and degrees of complexity, but they all serve a similar function: to eliminate the need to sort during the picking process. As a result, put walls drastically reduce the time it takes to execute a picking job.
How Do Put Walls Work?
Most commonly, put walls are a row of shelves and sorting totes along a straight wall, containing between 100-500 sorting bins. Batch pickers end their picking runs at this fixed put wall location and then sort their picked items into the appropriate sorting bins.
Advanced Warehouse Put Wall Systems
Some put wall systems are more advanced and include assistive technologies to support sorting operations. Put-to-Light solutions, for example, provide warehouse employees with a visual identifier (a light) when an item is scanned. This allows pickers to see what order the item belongs to and where to place it within the warehouse put wall without having to look at location labels.
Automated put wall systems use robotics and automation technology to scan, identify, and consolidate orders with little to no human input. These solutions are more costly to implement and generally require a more sophisticated WMS to oversee.
That said, they can provide efficiency gains of up to 10 times that of a manual process, as well as a great ROI when dealing with higher order volumes.
The “Mobile U-Shape Approach” is another advanced put wall method for operations that need a flexible, mobile system capable of dealing with varying order volumes.
In this model, pickers use moving shelves with about 25 totes per unit. Multiple “mobile sorting units” are brought together into a U-shape for increased consolidation capacity. With this model, batch pickers can pick mass amounts of items in one run, sort them in one aggregated step, and easily move the entire system to the packing station when ready.
Key Benefits of a Warehouse Put Wall
In addition to saving your operation time during the picking and packing process, put walls have a positive effect on labor efficiency and order fulfillment accuracy. Let’s look at this efficiency using the real-life stages of a workflow:
During the picking stage, more picks can be made in one run because sorting is deferred to a later step, allowing this phase to be completed even faster.
Sorting can be done in one aggregated bulk process instead of one by one, allowing this process to become more efficient as well.
Since the put wall sorting process is generally done in a space near a packing station, the packing phase can occur the moment a cell is full and ready for final processing (provided you have a system that can detect this).
In addition to aiding labor efficiency, certain types of put walls can also enhance your operational efficiency by minimizing space requirements. Plus, put walls boost order accuracy by allowing your employees to focus on one aspect of the picking, sorting, and packing process at a time.
Ease of training is another benefit because each stage of the picking and packing process is compartmentalized, making training and onboarding simpler.
This blog is part of Logiwa’s 15-minute QuickTake webinar series. To view the recorded Put Wall video, or any of our previous QuickTake sessions, visit: Logiwa Resource Page
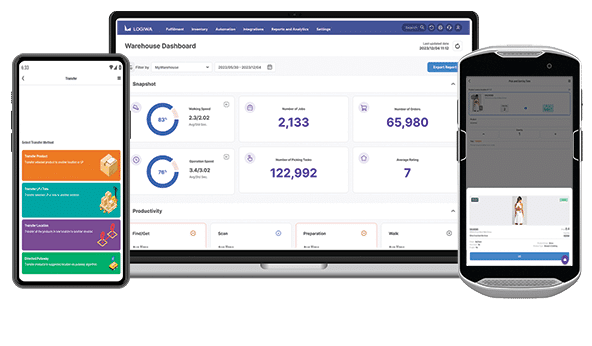
Things to Consider When Implementing a Warehouse Put Wall
The benefits put walls can offer fulfillment operations are clear, but making the switch to this type of system does take some planning. As your team deliberates whether or not to implement put walls within your warehouse, consider the following:
- Order volume
- Product dimensions
- Physical layout
Order Volume
The main reason a put wall system is preferred over a cluster-picking model has to do with order volume becoming too great for the existing system.
For example, consider fulfilling 100 orders with a cluster picking setup using carts of 10 totes. For those 100 orders, you’d need to make 10 trips. With a batch picking/put-to-wall system, you could pick all 100 orders in a single trip.
The tradeoff effort would be in the post-pick sorting process. But by using an efficient put wall system, that sorting would still happen more efficiently than doing it on the picking cart.
Product Dimensions
The primary efficiency driver behind put walls revolves around reducing the number of picking runs by picking more per trip. If your products are too heavy to increase the per-trip volume, this model might not work very well.
Physical Layout
Put walls require space, though the amount of space and whether that space is fixed or dynamic will vary depending on your implementation. Standard fixed put walls need a considerable amount of space and can’t be easily changed.
If you have a highly variable order volume, this could lead to an inefficient use of warehouse space. Automated put wall solutions are generally intended for very high-volume operations and typically require a lot of permanent space to install. A U-shape model allows for flexibility in space and mobility, however, there are still some space requirements.
With these elements in mind, let’s get into the process of implementing a warehouse put wall and making it work for your warehousing operations.
How to Get Started Using Put Walls
Now that you’ve decided to implement put walls into your fulfillment operations, here are a few best practices for getting started.
Step #1. Choose a Physical System
Choosing your ideal type of put wall largely depends on the considerations discussed in the previous section, like order volume, product dimension, or the amount of space you have available.
Fixed shelf and automated systems will require more space, while U-shape put walls offer more flexibility. No matter which you choose, it’s generally advisable to keep your put walls near your packing areas to help streamline your workflows.
Learn how Logiwa customers applied Put to Wall picking in their warehouses to transition from low to high volume fulfillment.
Step #2. Map Out Your Workflow Steps
Your system selection criteria may change based on unique use cases in your operation. For example, if you have multiple custom packing requirements or quality control steps as part of your process, some automated solutions may not work as well together.
In short, never implement a tool to support a task that you aren’t able to whiteboard or draw out on paper.
Step #3. Ensure Your WMS Can Manage Put Walls
Some WMS providers are better than others when it comes to working with put wall models. If you’re using a partially manual/paper-based system or a weaker WMS software that can’t handle your automated workflows, it may be difficult to reap the benefits of a put wall system.
Be sure to work with your WMS provider to understand if your current solution is compatible with a warehouse put wall solution.
Step #4. Outline an Implementation and Training Plan
For rapidly growing operations, adopting put walls can feel like a lot to oversee, so a strong training and rehearsal process is recommended.
This step should include your existing staff, as well as incoming new hires and seasonal employees. Consider providing some combination of in-person training, recorded training, and dry runs to ensure there are no hitches with the process.
Step #5. Create a Plan for Monitoring and Controlling
As with any new process, it’s important to understand your benchmarks and set goals. Tracking warehouse management system KPIs requires a good reporting solution, so make sure to identify your reporting needs and expectations before fully launching your put wall system. Otherwise, if you run into trouble, it could be difficult to identify where the problem lies.
Boost Warehouse Efficiency With Logiwa WMS
Logiwa has helped many of our customers implement put wall systems within their fulfillment centers. With the help of our cloud fulfillment software platform, countless businesses have been able to build a more robust fulfillment process. To learn more about our industry-leading solution, request a demo today!