Contents
Scaling DTC Operations Starts with Labor Management
Managing and operating a warehouse takes a lot of work and, more often than not, many workers. As a result, successful labor planning is one of the most critical processes for achieving successful high-volume, direct-to-consumer (DTC) operations. It is a time-consuming task that must consider all aspects of your fulfillment operations, technology use, and employees’ skills.
If your goal is to scale your DTC fulfillment operations, you need to ask yourself if your current workforce and labor plans align with that goal. Growing your business without first establishing proper warehouse staffing levels could drastically hinder your growth plans, resulting in a loss of profits and unhappy brands, retailers, and customers.
We’ve created a handy guide outlining five steps for successful warehouse labor planning but let’s go over a few of those steps.
Assessing Your DTC Operation’s Labor Needs
DTC fulfillment labor needs differ from other types of order fulfillment. In DTC fulfillment operations, order volume is typically higher, uses smaller packaging, is more time-sensitive, and requires very high accuracy rates. Scaling DTC fulfillment operations requires a great team.
When building your warehouse staffing plan for DTC operations, don’t forget to consider the following:
-
- What are the roles you need to run your warehouse safely and efficiently?
- What labor hours and shifts will you need to handle your expected orders?
- Are you planning in advance for seasonal fluctuations, such as Black Friday and Peak Season, that will require additional hiring and labor cost?
- Have you built into both your recruiting plans and budget the need for specialized certifications and training required for certain roles and for handling materials?
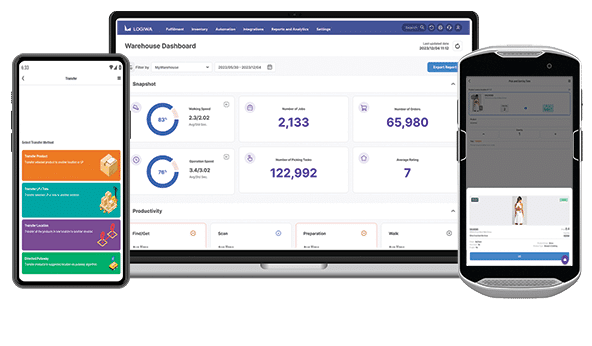
DTC Fulfillment Labor Forecasting
Effective warehouse labor forecasting can tell you when you need to hire more workers or when you need fewer workers. These peak seasons typically occur in the fall as retailers and brands ramp up for back-to-school, Halloween, and the holiday season. Depending on the types of brands and retailers you serve, you may need to hire more workers or add more shifts during peak season, and labor forecasting can help you manage these seasonal changes.
If your warehouse uses robotics to assist with picking (Robotics as a Service or RaaS), you’ll need employees who know how to work with those tools. However, a benefit of implementing robotics is that it can allow you to keep labor costs low as these tools can take over some tasks, such as picking, previously done by people. Additionally, some warehouse operators see lower turnover and a greater ability to attract employees when they can work with technological support.
If you have some less productive shifts or plan to add more shifts, finding employees who can drive productivity to meet operational goals could be a priority in your warehouse staffing plan.
Being flexible in your workforce management is key for scaling DRC fulfillment operations. Your clients may decide to have a last-minute sale that requires more employees for a short time. Having enough staff can also help when employee illness or other reasons for being absent occur, allowing you to maintain consistent operations to meet customer demand.
Managing Temporary Employees with WMS Software
With temporary workers and increased volume, a learning curve is inevitable. Your warehouse management software can help reduce the learning curve when onboarding and training temporary employees, allowing you to keep your warehouse efficiency high.
Learn more about seasonal employment and how it impacts warehouse labor planning.
Using Labor Analytics for Warehouse Staffing
Warehouse management system (aka WMS software) is an excellent tool for labor management. With access to historical data on employee efficiency, busy seasons, and even employee skills and competencies, you can create a comprehensive warehouse staffing plan that suits your needs year-round.
If you are experiencing slowdowns or a higher error rate in your packing areas, you may need to invest some time in training or hiring additional employees to work in that area.
Including wms key performance indicators (KPIs) to track in your labor management plan will allow you to monitor employee performance and error rates and to make process improvements before they become too big of an issue.
Without employees, inventory wouldn’t enter your warehouse, and orders wouldn’t be filled. An effective warehouse staffing plan is essential if you’re looking to scale your DTC fulfillment operation. Your plan will help you ensure you have the qualified employees you need when you need them, to meet your client and customer demands. Warehouse software can help.
Download our Warehouse Labor Planning Template to help you estimate the number of workers and labor hours you will require for picking and packing. If you have more questions, reach out to a member of our team or request a demo.