What fulfillment trends can logistics operations expect in 2024?
Musaoglu: In 2024, there will be more advancements in technology and adjustments to consumer behavior. These advancements and adjustments will build on trends from this year. Logistics will see more automation, sustainability, personalization, micro-fulfillment centers, and data-driven strategies to boost labor efficiency.
- Given the escalating labor shortages throughout the fulfillment sector, there will be increased emphasis on automation and robotics adoption. This trend is crucial for reducing reliance on manual labor and enhancing operational efficiency. Both are key to meeting today’s highly competitive fulfillment standards.
- As environmental consciousness is something customers expect, sustainability will be another major focus across the ecommerce businesses. Eco-friendly packaging and green logistics not only meets growing environmental regulations but consumer demands for sustainable practices.
- Enhanced personalization has become hugely important for creating a positive shopping experience for consumers. As a result, personalization will become even more sophisticated in 2024—focusing on catering to individual consumer preferences and expectations. This will require operations to understand and respond to unique customer needs as they shape their fulfillment process.
- The rise of urban micro-fulfillment centers is expected to continue, driven by the need to expedite delivery and reduce logistics costs, particularly in densely populated areas.
- Finally, leveraging big data analytics and AI will be critical for optimizing inventory management, demand forecasting, labor planning, and enhancing the overall customer experience. This approach will become increasingly important for making informed, strategic decisions in fulfillment operations and improving labor efficiency. In 2024, technologies and strategies that enhance productivity, reduce labor-intensive tasks, and streamline operations will continue to help mitigate the impact of labor market challenges.
These trends collectively emphasize the need for efficiency, sustainability, and adaptability in meeting the evolving demands of the market and the workforce. Those are the big trends I see shaping logistics operations in 2024.
How is Artificial Intelligence (AI) impacting the modern fulfillment logistics industry?
Musaoglu: AI is really transforming the fulfillment logistics industry, and it’s happening in a variety of ways.
First off, AI enables quicker and more efficient decision-making processes, especially in complex logistics environments. This extends across the supply chain, enabling timely and precise responses to operational needs. Additionally, predictive AI plays a crucial role in demand forecasting, allowing businesses to proactively optimize their inventory levels based on customer demands in real-time.
Another significant area where AI is making strides is in optimizing delivery routes. It not only accelerates delivery times but also substantially cuts down on transportation costs. In warehouse operations, AI leverages vast data to enhance the efficiency of picking and packing processes, manage labor more effectively, and streamline shipment preparations. By automating routine tasks, reducing errors, and freeing up human workers for more complex tasks, AI is adding substantial value to the operational workflow.
In essence, AI is more than just a technological upgrade; it’s a game-changing force that is reshaping the fulfillment logistics landscape. It is also carving out new strategic advantages, positioning businesses to thrive in an increasingly competitive industry.
Do you believe AI determines the success or failure of fulfillment networks, online sellers, 3PLs, brands and retailers?
Musaoglu: Yes. Especially in the days ahead, AI will play a critical role in determining the success or failure of fulfillment networks, online sellers, 3PLs, brands, and retailers. The use of AI in these sectors has transitioned from being a competitive advantage to a necessity—particularly in the context of operational efficiency and customer satisfaction.
Logiwa has observed remarkable increases in productivity when using AI to create jobs for pickers and packers. By leveraging AI, we have seen productivity enhancements ranging from 30% to 60%. This substantial improvement is not just a metric—it represents a transformation in how fulfillment processes are executed.
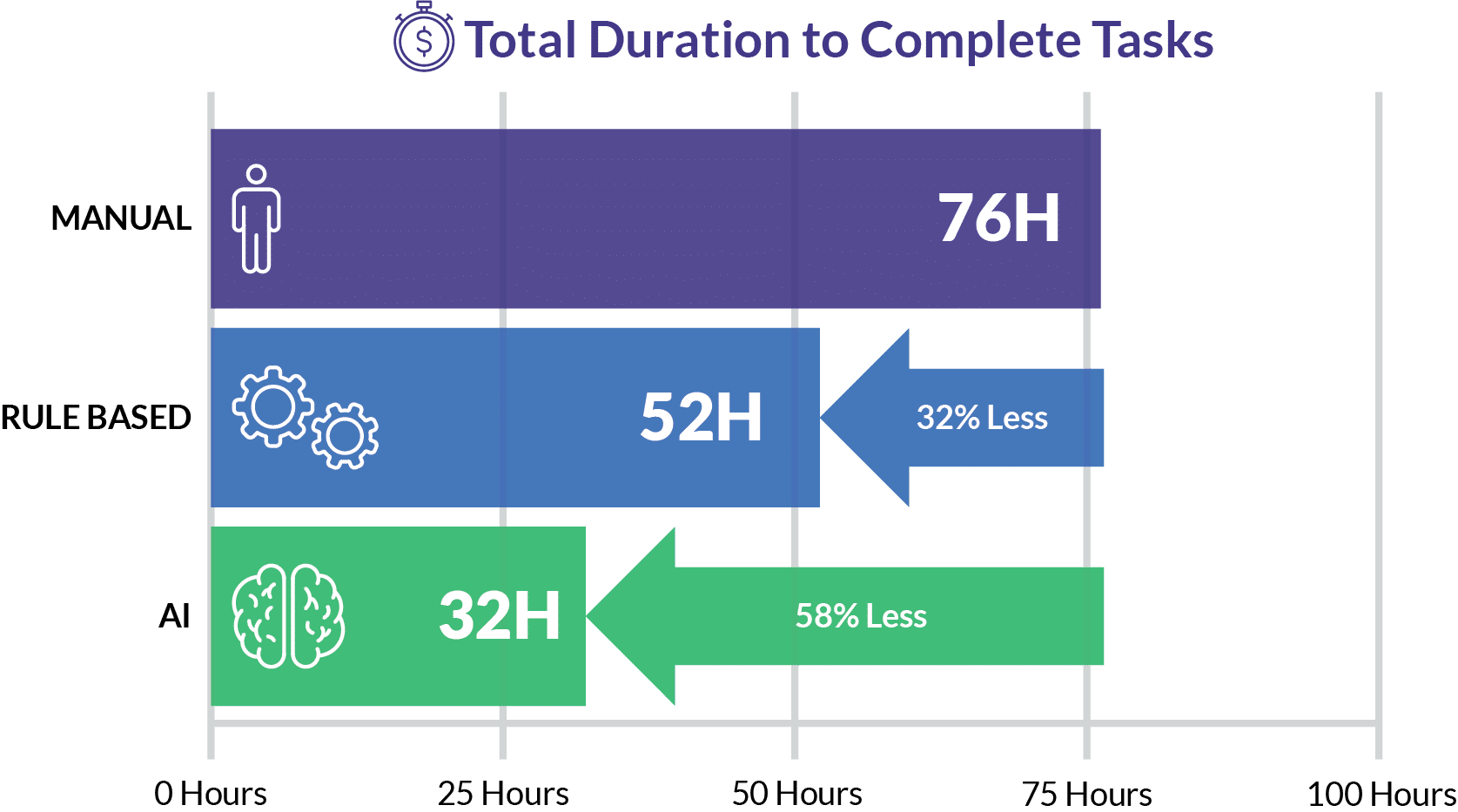
How is AI used to create picking and packing jobs? Where does that 30% to 60% improvement come from?
Musaoglu: In a high-volume fulfillment center, the traditional method of assigning tasks to pickers and packers is based on manual planning and rudimentary software algorithms. This process is inefficient and leads to longer processing times and higher error rates.
When we implement an AI-driven system to create and assign picking and packing jobs, the AI algorithm analyzes various factors (such as item locations, order priority, and worker availability) to optimize task allocation.
More efficient route planning for pickers, reduced time spent per task, and a significant decrease in errors is what leads to a 30% to 60% increase in productivity. Additionally, AI is able to help operations adapt to real-time changes in inventory and orders, ensuring ongoing efficiency gains.
This improvement in productivity not only enhanced operational efficiency but also translated into faster order fulfillment, higher customer satisfaction, and reduced labor costs.
How is WMS technology evolving based on these types of advancements and trends?
Musaoglu: WMS technology is evolving by embracing AI and Machine Learning This technology is enabling predictive analytics and highly effective decision-making, which enhances visibility across the supply chain and facilitates more intelligent process optimization.
Another key development is the shift towards Cloud-based solutions, which ensures scalable, accessible, and more cost-effective fulfillment management. It’s particularly beneficial for businesses looking to adapt and grow without the constraints of traditional software systems.
I’d say we’re also seeing a trend towards more mobile and user-friendly interfaces, as well as greater interoperability. This evolution is crucial as it aligns with the need for on-the-go management, catering to the modern workforce that values efficiency and accessibility.
Today’s WMS technology is increasingly designed to seamlessly integrate with other critical systems like Transportation Management Systems (TMS), Enterprise Resource Planning (ERP) systems, and ecommerce platforms. This is essential for creating a cohesive and efficient fulfillment ecosystem.
What is a Fulfillment Management System (FMS)?
Musaoglu: A Fulfillment Management System (FMS) is a comprehensive software solution that integrates various aspects of fulfillment, from order management and inventory control to warehousing operations like picking, packing, and shipping.
FMS excels in real-time inventory management to optimize stock levels and avoid overstock or stockout scenarios. It streamlines order processing across multiple channels, and enhances warehouse operations through layout optimization and the integration of automated systems. This reduces the time and cost of fulfilling each order.
An FMS also plays a pivotal role in shipping and logistics. It offers tools for carrier selection, label generation, and package tracking. This not only boosts operational efficiency but also significantly enhances customer satisfaction by ensuring prompt, accurate deliveries and a transparent fulfillment process.
Why is a FMS more beneficial to operations than traditional WMS?
Musaoglu: While a traditional Warehouse Management System (WMS) plays a crucial role in optimizing warehouse operations, a Fulfillment Management System (FMS) takes this a step further by offering a more holistic and integrated approach to the entire order fulfillment process.
An FMS extends beyond the boundaries of a warehouse. While a WMS focuses primarily on optimizing the storage and movement of goods within a warehouse, an FMS encompasses the end-to-end process—from the moment an order is placed to the final delivery to the customer. This includes inventory management across multiple channels, order processing, picking, packing, shipping, and even returns. By managing these interconnected components, an FMS provides a more comprehensive solution for businesses looking to streamline their entire fulfillment operation, not just their warehouse activities.
Moreover, an FMS is inherently designed for the complexities of today’s omni-channel retail environment. It excels in integrating with various ecommerce platforms, marketplaces, and other sales channels. This integration ensures real-time synchronization of inventory and orders across all channels. In contrast, traditional WMS solutions might not offer the same level of integration and real-time data visibility across multiple sales channels.
What inspired the development of Logiwa IO?
Musaoglu: Logiwa was inspired by the need to assist companies in launching, growing, and scaling their high-volume fulfillment operations. The shift towards online shopping and the complexities associated with fulfilling direct-to-consumer orders necessitated a more dynamic, flexible, and technology-driven solution.
Logiwa IO was developed to meet these evolving demands, particularly in the face of the challenges posed by traditional warehouse management systems (WMS) which were not adequately equipped to handle the rapid dynamics of online sales and direct-to-consumer fulfillment requirements.
What sets Logiwa IO apart from other solutions?
Musaoglu: From the very beginning, our vision for Logiwa IO was to create a product that is rooted in customer feedback and real-world logistics challenges. This customer-centric approach is fundamentally what differentiates Logiwa IO from other solutions in the market.
At Logiwa, we believe that the best insights come from those who are on the front lines of the industry. Therefore, we’ve built a continuous feedback loop into our development process. This means that our software is not just designed by us—it’s co-created with the input, experiences, and needs of our customers. This collaboration has allowed us to tailor Logiwa IO to address the specific pain points and operational challenges faced by businesses in the warehousing and fulfillment sectors.
One of the key outcomes of this approach is the high degree of customization and flexibility that Logiwa IO offers. We understand that no two businesses are the same, and our solution reflects this. Whether it’s adapting to unique workflow requirements, integrating with a diverse array of ecommerce platforms and marketplaces, or scaling to meet the growing demands of a business, Logiwa IO is designed to be highly adaptable.
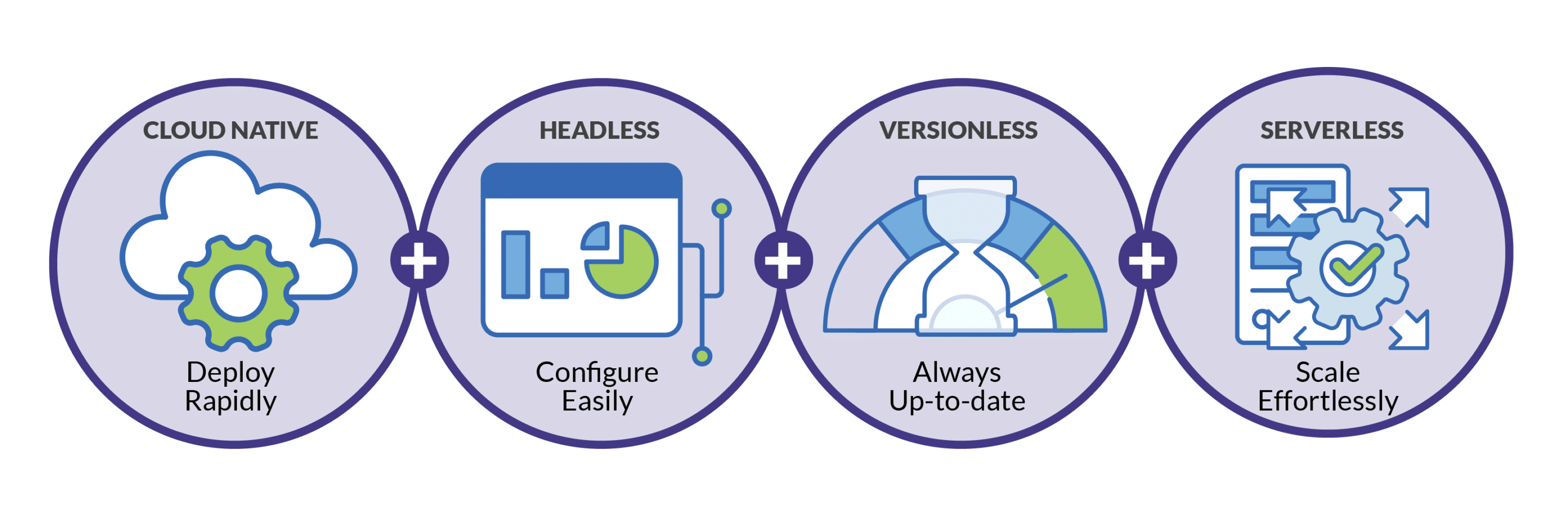
What developmental achievements are you most proud of?
Musaoglu: There’s a lot that comes to mind, but I think our advancements in AI are what I am most proud of. Logiwa IO’s AI algorithms analyze vast amounts of data to optimize operations—from predicting the best inventory layout to enhancing picking and packing jobs while employees are actively on the floor.
Improving labor standards is another enormous accomplishment for our team. We understand that the human element in warehousing and logistics is invaluable. Logiwa IO is designed to maximize the productivity of the available workforce—while simultaneously reducing the physical strain on workers. By streamlining tasks and reducing manual labor through intelligent automation, we’re helping businesses create a more sustainable environment with higher rates of employee satisfaction.
The UX/UI of Logiwa IO is another aspect of the solution I’m extremely proud of. Logiwa believes that powerful technology should also be user-friendly. Our platform’s interface is designed to be intuitive and easy to navigate, ensuring that all levels of users, from warehouse staff to management, can quickly adapt and make the most of our system. This focus on user experience helps in reducing training time and enhances productivity from day one.
What makes Logiwa IO a future-ready solution?
Musaoglu: Logiwa IO embraces headless architecture, and that is a feature that truly sets us apart. This approach allows for greater flexibility and scalability. It enables businesses to integrate Logiwa IO seamlessly with their existing systems and ecommerce platforms. By providing a solution that fits into the unique tech ecosystem of each business, rather than forcing them to adapt to ours, users gain a new level of flexibility that is crucial in today’s fast-paced, ever-evolving digital landscape.
How will Logiwa continue evolving to tackle today’s changing market conditions?
Musaoglu: Logiwa is committed to evolving continuously to address the dynamic market conditions of today and the future. Our approach is multi-faceted, focusing on advancements in AI, global expansion, and a steadfast commitment to incorporating customer feedback into the development of Logiwa IO.
As a company, we will continue to develop even more sophisticated AI capabilities. This includes advanced predictive analytics for better demand forecasting, AI-driven optimization for warehouse operations, and even more intelligent automation in areas like inventory management and order processing. Our goal is to provide a system that’s not just reactive, but proactively anticipates and adapts to changes in the market.
As previously mentioned, Logiwa is actively working to broaden its footprint. We understand that each market has its unique challenges and opportunities, and our strategy involves tailoring our solutions to meet these diverse needs. This expansion isn’t just geographical; it’s also about expanding the range of industries and business sizes we cater to.
We will continue to incorporate customer feedback as our product and the market evolve. We believe that our customers are the best resource for understanding the market’s needs and challenges. Therefore, we have established robust channels for gathering and analyzing customer insights.
This feedback is not just a one-way street; it’s an ongoing dialogue that helps us continuously refine and extend Logiwa IO’s capabilities. Whether it’s enhancing user experience, adding new features, or improving existing functionalities, our customers’ voices are always at the forefront of our development process.
Elevate Your Fulfillment Network’s Efficiency with the Power of AI
Warehouse Management
Modern digital WMS powers a modern fulfillment experience