Order picking is a crucial warehouse process that accounts for a large amount of a warehouse’s labor costs. Also, manually picking heavy items causes many injuries on warehouse floors. Even worse, warehouses are currently dealing with a labor shortage, which means finding qualified staff for order-picking roles is a serious challenge.
Fortunately, whether you’re a B2B, direct-to-consumer (DTC), or hybrid warehouse service provider, you can resolve many of the above issues with automated warehouse picking.
In this guide, we’ll discuss automated warehouse picking and how it can benefit your warehouse. We also reveal how you can introduce picking automation within your organization.
What Is Automated Warehouse Picking?
Warehouse picking traditionally involves humans locating and collecting items manually from storage to fulfill customer orders. Automated warehouse picking, on the other hand, involves using robotic or semi-robotic technologies to handle or assist the picking process. It streamlines and optimizes picking by shortening walking time and picking routes.
For example, instead of workers navigating your warehouse to locate and retrieve items, autonomous mobile robots (AMRs) can retrieve specified items. The robotic system will then deliver the collected items to humans to process them for order fulfillment.
Several automated picking solutions are available, and you can pick one that keeps human involvement in the picking process to a minimum. We recommend selecting an automated warehouse picking solution that can integrate into your existing warehouse processes quickly and seamlessly. The technology should also be compatible with your WMS and preferred order-picking method.
How Does Automated Warehouse Picking Work?
A successful automated warehouse picking setup requires combining effective picking software and hardware. For example, the picking software determines the picking path and method the hardware must use to retrieve and drop off collected items.
Industry-leading warehouse management systems (WMS), such as Logiwa WMS, come prepackaged with such features. Besides managing item retrievals, a comprehensive WMS can help manage order receipt and prioritization, inventory updating, and labeling.
The other half of automated warehouse picking is the hardware. Depending on your warehouse and preferred level of automation, your hardware may include
-
- Autonomous Mobile Robots (AMRs): These automated robots navigate the warehouse to retrieve items and deliver them to pickers. The pickers then process the items to fulfill orders.
- Automated Storage and Retrieval Systems (AS/RS): These systems use computer-controlled carousels or vertical lift modules (VLM) to retrieve items from storage locations. Retrieved items go into an AMR or AGV that delivers them to a picker.
- Conveyor Systems or Automated Guided Vehicles (AGVs): A conveyor system or AGV autonomously delivers items to pickers, eliminating walking time. However, these systems can’t retrieve items from storage. They need a human or robotic picker to retrieve an item and place it in them for delivery to the sorting area.
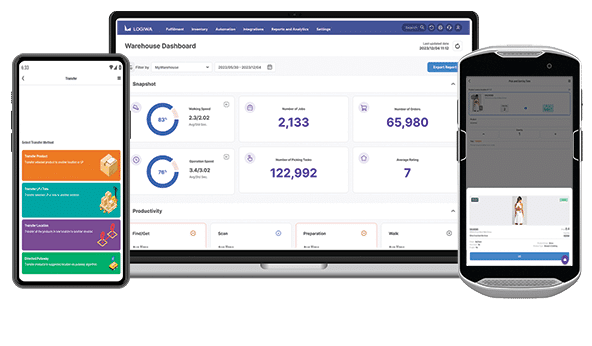
Combatting the Ongoing Labor Shortage With Automation
In 2022, 73% of warehouse managers couldn’t find enough workers, and the problem persists to date. Warehouses serving businesses that take online orders are among the hardest hit due to online shopping, which peaked during COVID and is still growing.
The lack of warehouse workers to pick, pack, and fulfill the increasing number of orders has led to delayed deliveries, overwhelmed workers, and other issues. Forward-thinking companies are successfully combating such issues with warehouse automation.
The goal of warehouse automation isn’t to completely replace workers. Instead, the goal is to supplement physical labor by automating repetitive and labor-intensive tasks. Automating such tasks allows warehouses to operate smoothly and efficiently with fewer workers (less reliance on human labor).
Besides helping you make up for labor shortages, automation can make your warehouse more attractive to potential hires.
Other Benefits of Automated Warehouse Picking
The benefits of automated warehouse picking don’t stop at helping with labor shortages. Automating can also improve warehouse operations in the following ways.
-
- Minimize workplace accidents and injuries: Operating forklifts and manually moving heavy items are among the leading causes of warehouse accidents and injuries. Automating inventory storage and picking with AMVs and AMRs will reduce the risk to warehouse workers, leading to a safer workplace.
- Boost savings and profitability: Automated warehouse systems can work tirelessly, and you don’t need to pay them salaries. So, automating more of your warehouse can help reduce labor costs and boost profitability by increasing your facility’s uptime. Also, the average warehouse worker spends 80% of their shift on non-revenue generating tasks, such as walking between storage and sorting areas. Automated warehouse picking streamlines the picking process, reducing workers’ walking time so they can focus more on revenue-generating tasks.
- Faster order fulfillment: Automated picking systems facilitate quicker item retrieval, sorting, and packing, leading to faster order shipment and delivery. Fast and accurate order fulfillment leads to happy customers, which is great for business.
- Real-time inventory management: Automated picking systems integrated with a WMS provide real-time inventory tracking and management. Insights and alerts provided by an inventory tracking and management tool can help prevent costly stockouts or overstock situations.
- Scalability and flexibility: Instead of hiring more workers to cope with spikes in demand or traffic in your warehouse, you can have a scalable automated picking system. You can adapt scalable, automated warehouse systems by reconfiguring picking processes to keep up with demand increases or decreases at no extra cost.
How Logiwa Can Support
Installing a robotics system isn’t enough to automate your warehouse’s picking process. You need a warehouse management system to control and monitor your robots. Logiwa WMS is the all-in-one WMS for turning your traditional facility into a fully digital warehouse.
Our WMS software can increase your labor efficiency by up to 40%, eliminating issues such as low productivity and excessive human errors. The software comes ready to use out of the box with pre-built automation rules to quickly automate and optimize your picking, packing, and shipping processes.
Also, Logiwa’s integrations process makes connecting to your favorite shipping, accounting, robotics, and ecommerce solutions seamless.
Automate Your Warehouse With Logiwa
Over-relying on human labor to run your warehouse won’t give you a competitive advantage in today’s world. Supercharge your facility by switching from manual to automated warehouse picking.
By automating picking, packing, and shipping, you can minimize human error, save money, and boost efficiency within your warehouse
Take your first step toward automating your warehouse with Logiwa. Our warehouse management software gives you the power to automate your processes and monitor your automated systems from a single device. Request a demo of Logiwa WMS today!
Ship more with a fully integrated WMS Software that connects with 200+ e-commerce
Warehouse Management
Modern digital WMS powers a modern fulfillment experience