Key Takeaways:
- Risk assessments aim to identify potential dangers that can impact business operations, inventory value, and employee safety, and then implement protective measures.
- Different types of risk assessments include evaluating facility hazards, assessing system efficiency, and verifying integration accuracy.
- The frequency of warehouse risk assessments can vary, but they should be conducted before peak seasons and after major operational changes.
- Leading Warehouse Management System (WMS) solutions, like Logiwa, utilize AI and cloud-based platforms to optimize processes and reduce risks in warehousing.
- Regular risk management, aided by advanced technology, ensures smoother and safer operations, especially during high-demand periods.
When it comes to modern order fulfillment, risk management is a critical component to achieving successful warehouse operations and dependable supply chains. Unfortunately, many fulfillment providers underestimate the importance of conducting regular risk assessments and do not perform them as frequently as they should.
Since warehouses and distribution centers are complex, living environments, they come with their own unique risks and hazards to keep track of. From maintaining warehousing facilities and machinery to monitoring inventory accuracy and data accessibility, there are plenty of opportunities for issues to arise.
Luckily, the most common operational risks faced by third-party logistics (3PL) providers, online retailers, and brands can be avoided by conducting frequent risk assessments and by leveraging competitive warehousing technology. But how often should you audit your warehouse operations for potential problems? And what should you be looking for?
In this blog, we will discuss:
The Importance of Warehouse Risk Assessments
As the demands of ecommerce have increased, so has the need for safe and efficient fulfillment networks. Even with the aid of high-efficiency WMS technology, all fulfillment services overseeing warehouse operations face some amount of risk. That is why maintaining regular risk assessments and visibility into your facilities and software solutions is so important. It ensures you aren’t experiencing currently having any problems and aren’t setting yourself up for any in the future, either.
After all, one overlooked environmental hazard or data discrepancy can lead to Occupational Safety and Health Administration (OSHA) violations, failed SLAs, lost profits, and damaged brand credibility. Without conducting frequent risk assessments, your warehouse runs a higher chance of: employee injuries and facility accidents, damaged or broken inventory, compliance violations (and fines), efficiency setbacks, and other unforeseen costs.
As a final note: risk assessments should not become secondary to your other fulfillment goals (ex. maximizing throughput and customer satisfaction), nor should they be conducted less regularly because you have a WMS powering your operations. WMS platforms, like all forms of technology, have limitations and cannot see all ends of an operation. Consistent risk audits are the only way to guarantee you are on top of managing your operational risks.
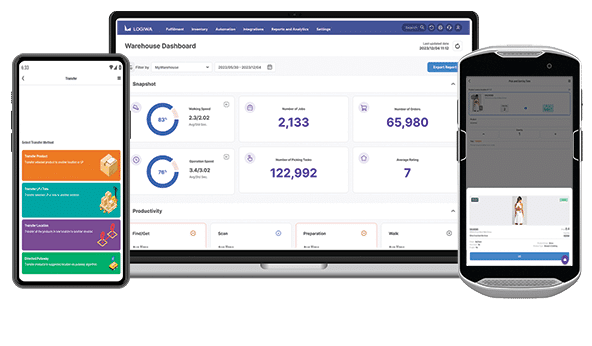
The Goal of Risk Assessments for Warehouse Operations
A risk assessment, or risk audit, seeks to eliminate potential dangers that have the ability to damage your business operations, cause inventory to lose value (or become unsellable), or risk the safety of employees. Before we talk about how often to conduct them, it is important to clarify that there are different types of risk assessments, and all of them should include two steps: identifying hazards and putting protective measures in place to resolve them.
The key reasons to conduct risk assessments, include:
-
- Keeping warehouse staff safe and facility standards maintained
- Avoiding compliance-related fines and litigation claims
- Safeguarding inventory and shipping materials from damage
- Improving resource management for long-term efficiency (adding in controls)
- Increasing warehouse productivity by rooting out system inefficiencies
Let’s break down three avenues for risk assessment that best service warehouse operations and what the benefits of each are.
Types of Risk Assessments to Conduct
In addition to a standard risk audit of your facility, which is required by most states, and OSHA requirements like annual employee safety training, you will want to take time to carry out several primary risk assessment initiatives at various points throughout your sales cycles or before peak seasons.
Facility Hazards
This includes identifying hazardous materials, rack damage, areas where lifting items or movement is inhibited, and other environmental factors that put efficiency, personal safety, or inventory at risk. When these types of hazards are identified, you are expected to acknowledge and resolve them as quickly as possible or face significant fines. No matter what the risk is, you must find a way to remove it, provide an alternative to neutralize it, reduce exposure to it, or change your warehouse processes in some other way to eliminate all potential risks.
For more insights on facility safety, check out Logiwa’s comprehensive blog, “The Warehouse Owner’s Guide to Warehouse Safety.”
System Efficiency
Assessing risks of inefficiency have to do with how well your actual workflows and automation processes are going in your warehouse. Does the inventory data in your WMS match your physical inventory? Is your stock control systems failing to register replenishment needs? Are there bottlenecks forming due to the placement of your sorting or packing stations? Eliminating these inefficiencies will help reduce the risk of inventory shortages, delays in order deliveries, and disorder on your warehouse floors.
Integration Accuracy
Identifying risks in relation to integrations is a matter of verifying that your WMS is pulling the data from your integration partners, so both systems are in sync. An example of this might be checking that your inventory data matches the availability shown in your online stores. Another example could be running a report on order processing / delivery accuracy. If your WMS is failing to generate the correct picking orders, route orders efficiently, or ship items to the right buyer based on the information coming in from your integrations, you will have identified a major pitfall for your business.
How Often to Conduct Warehouse Risk Assessments
According to some industry sources, an annual risk assessment is enough. Others suggest a weekly or quarterly review to ensure success, depending on the speed of your inventory turnover. But a more definitive answer might be this: no one knows your operations better than you do. When would a warehouse risk audit benefit your operation the most? How often do you think your individual operation needs to be re-assessed based on the data you have?
Regular inventory counts, or cycle counting, is one form of risk management… but conducting a full risk assessment of your facility and automation processes is a much bigger task depending on the size of your operation. As you you formulate a customized risk assessment strategy for your business, here are some things to keep in mind:
-
- Risk audits should be carried out before peak seasons in order to ensure smoother and safer operations as order volumes increase and processes speed up. The last thing you want is to be scrambling to handle facility breakdowns, employee injuries, and data mishaps in the middle of your busiest fulfillment periods.
- Scale the number of risk audits you do based on how your operation evolves. If you are growing in size, taking on new clients, expanding your inventory, or changing up technology solutions, you may want to conduct an additional risk audit after each major milestone to ensure you’re starting each new stage of your journey on the right foot with clean data.
- Maintain risk management year-round using technology. Leading WMS solutions can help fulfillment operations lower operational risks with intelligent software and embedded reporting and analytics tools can help you flag issues or identify weaknesses in your overall organization. Plus, with cloud-based solutions, you can maintain live insights into the health of your entire fulfillment network right from your mobile device.
How WMS Software Helps Reduce Risks
Logiwa recognized the importance of optimizing processes like inventory management in order to improve the safety and efficiency of modern fulfillment warehouses. Our cloud-based WMS platform utilizes AI-powered algorithms to help our clients make the most of their warehouse space, accomplish walking path optimization (to minimize the physical strain on employees), and risk management using cloud visibility and industry-leading automation.
Learn more about Logiwa’s smart materials handling or request a non-commitment demo to see why high-volume DTC warehouses all over the world have made Logiwa WMS their trusted fulfillment partner.
FAQs: Warehouse Risk Assessment
Q: What is the primary goal of a Warehouse Risk Assessment?
A: A Warehouse Risk Assessment aims to identify and eliminate potential dangers that can harm business operations, devalue inventory, or jeopardize employee safety.
Q: Why is it essential to conduct Warehouse Risk Assessments regularly?
A: Regular Warehouse Risk Assessments ensure the safety of warehouse staff, maintain facility standards, safeguard inventory from damage, and enhance overall operational efficiency by identifying and rectifying system inefficiencies.
Q: What are the different types of Warehouse Risk Assessments mentioned in the article?
A: The article highlights three main types: assessing facility hazards, evaluating system efficiency, and verifying integration accuracy within the warehouse management system.
Q: How often should businesses conduct a Warehouse Risk Assessment?
A: The frequency can vary based on individual operations, but it’s recommended to conduct assessments annually, before peak seasons, and after significant operational changes.
Q: How can Warehouse Management System (WMS) software like Logiwa help in reducing risks?
A: Logiwa’s cloud-based WMS platform uses AI-powered algorithms to optimize warehouse space, streamline walking paths, and manage risks using cloud visibility and industry-leading automation, ensuring a safer and more efficient warehouse environment.
Run a digital fulfillment network and grow your DTC business–without additional headcount
Warehouse Management
Modern digital WMS powers a modern fulfillment experience